Una soluzione dirompente
Nel processo di riciclo dello scarto pulper proveniente dalla carta da macero
I processi produttivi delle cartiere sono spesso additati come attività inquinanti e poco sensibili all’ambiente, ma grazie alle continue innovazioni tecnologiche, sviluppate nel settore negli ultimi anni, si trovano anche esempi degni di nota come il progetto del recupero delle plastiche leggere nello scarto pulper derivato dalla lavorazione della carta da macero.
Il progetto ZWP ha visto il suo completamento dopo due anni di prove e di test, installando un impianto completo presso lo stabilimento Smurfit Kappa Group (Ex BURGO GROUP) di Verzuolo CN, portando l’azienda ai vertici della sensibilità e della sostenibilità ambientale.
La società realizzatrice della soluzione è Hydroswiss, che dopo diversi mesi di studi e di prove è riuscita a convertire le plastiche leggere, rifiuto identificato con codice CER, in materia prima seconda, ovvero granulo plastico rispondente alla normativa UNI 10667.
Ma procediamo con ordine. La lavorazione della carta da macero produce uno scarto, chiamato scarto pulper, proveniente dalla prima fase di spappolamento della carta che avviene appunto all’interno del pulper. La percentuale dello scarto dipende ovviamente dalla qualità del macero utilizzato, arrivando anche al 10% del totale in caso di utilizzo di carta proveniente dalla raccolta differenziata municipale.
Da sempre lo scarto pulper, per la cartiera, è un vero problema sia economico sia ambientale. Il quantitativo di elementi non desiderati che compongono la carta da macero raccolta, varia in base alla provenienza, ma nonostante gli sforzi dei recuperatori, è sempre molto significativo.
La necessità di evitare il più possibile lo smaltimento, dovuto ai suoi costi in continua crescita, unitamente alle difficoltà oggettive della conversione in energia delle frazioni plastiche, mediante combustione, trovare una soluzione alternativa ed efficace per il riciclo di queste ultime è senz’altro un obiettivo ambizioso e allo stesso tempo un’esigenza incombente.
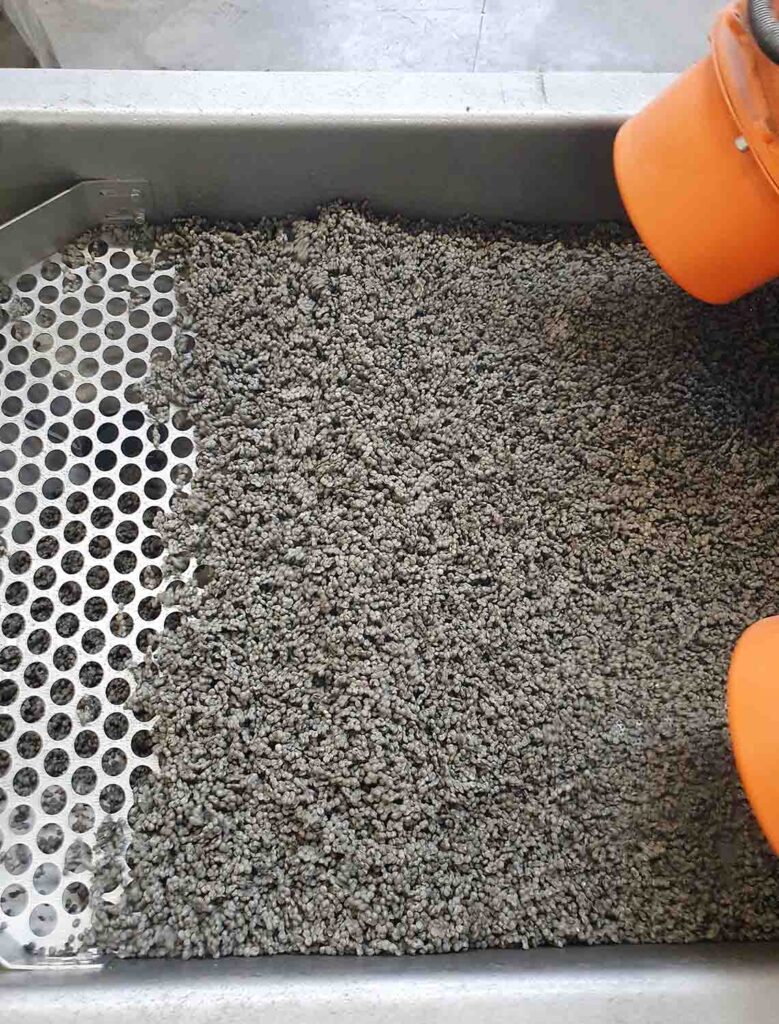
Scarto pulper trasformato in granulo plastico nella fase di vagliatura
La soluzione dirompente è stata quella di riuscire a soddisfare sia le richieste economiche della cartiera sia quelle di salvaguardia dell’ambiente. Mediante il processo innovativo ZWP, lo scarto pulper viene trasformato in materie prime secondarie (MPS) utilizzando esclusivamente processi meccanici a freddo senza utilizzo di sostanze chimiche aggiunte, a eccezione dell’ultimo processo di trafilatura che avviene a temperature intorno ai 200°C per poter fondere le plastiche.
Partiamo dal risultato. Lo scarto pulper tal quale è composto essenzialmente da acqua, metalli, plastiche, tessuti, legno, gomme e altri inerti. Il rifiuto entra nell’impianto di trattamento e di riciclo, dove sottoposto a varie fasi, circa una ventina in totale, viene lavato, uniformato, rilavato e man mano vengono separati i vari materiali riciclabili in: metalli ferrosi, acqua contenente fibra di carta e plastiche leggere (PE e PP); dai restanti elementi non riciclabili quali: inerti, plastiche pesanti e metalli non ferrosi. Questi ultimi se presenti in quantità significative si possono ulteriormente estrarre dallo scarto e riciclare. Il risultato quantitativo dipende dalle percentuali dei vari elementi in ingresso all’impianto, ma mediamente la frazione rimanente destinata al riciclo è del 10-15% riuscendo a recupere l’85-90% del rifiuto tal quale.
Il processo di trattamento. Essenzialmente il processo di lavorazione dello scarto pulper è suddiviso in due macro fasi. La prima consiste in diverse lavorazioni di lavaggio e di riduzione volumetrica dalle quali vengono separati i metalli ferrosi dai metalli amagnetici, oltre a tutti gli inerti e le plastiche pesanti di grande formato. Tutte le fasi sono addizionate di acqua di processo per effettuare un lavaggio efficace e poter recuperare la fibra di carta, la quale viene raccolta nei canali di scolo posizionati sotto i macchinari e fatta confluire in un serbatoio, previa filtrazione, per essere utilizzata successivamente come alimentazione dei pulper nella fase di spappolamento delle balle di macero.
Negli ultimi stadi della prima fase, il materiale flottante composto principalmente da plastiche, legno, gomma, sughero e da piccole parti di tessuto e di alluminio, viene sottoposto a ulteriore lavaggio con acqua di processo pulita per poi essere avviato a successiva separazione. Questo ultimo stadio di separazione permette la suddivisione delle particelle rimanenti di plastiche pesanti (PVC) da quelle leggere (PE-PP). Le prime sono indirizzate a smaltimento, mentre le seconde continuano il processo di trattamento dove avviene la separazione dal legno e infine sottoposte ad una fase di asciugatura.
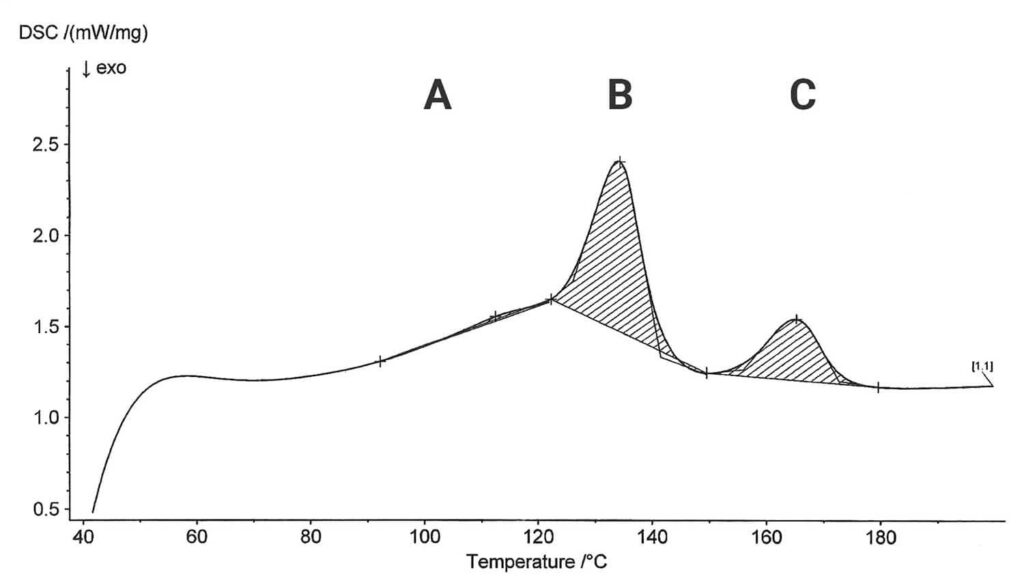
Analisi DSC:
A. 1% LDPE,
B. 63% HDPE,
C. 36% PP
Il materiale in uscita dall’impianto della prima fase di trattamento è formato da coriandoli con pezzatura di 20-30mm composti essenzialmente per il 90% da plastiche leggere e da un 10% di materiali indesiderati residui come legno, sughero e qualche particella di alluminio. Il materiale in questo punto è considerato ancora rifiuto, anche se non pericoloso, identificato con codice CER191204 o CER150102 in base alle procedure della cartiera.
La seconda fase di trattamento consiste nella trasformazione effettiva del rifiuto residuo in granulo plastico rispondente alla normativa UNI10667-15, vera e propria materia prima secondaria vendibile. Mentre nella prima fase di trattamento si sono dovuti progettare alcuni macchinari non esistenti sul mercato, in questa seconda fase si sono utilizzati macchinari esistenti ai quali sono state applicate opportune modifiche per poter processare le plastiche in uscita dal primo impianto.
Anche questa fase è composta da diversi stadi (nove) per poter convertire il rifiuto plastico in materia prima seconda sotto forma di granulo. Il materiale in ingresso viene sottoposto a un controllo mediante un metal detector per evitare che entrino nel processo particelle metalliche indesiderate. Successivamente il materiale entra in un densificatore che ha la duplice funzione di trasformare i coriandoli da 20-30mm in particelle ancora più piccole e uniformi oltre a ridurre l’umidità sotto il 5%, valore massimo desiderato negli stadi di lavorazione successivi.
Dal densificatore il materiale plastico viene dosato, mediante una valvola a lama controllata, nella vite di estrusione dove avviene la fusione. Anche la vite di estrusione, a sua volta, ha cinque fasi in sequenza: prima fase di compressione, prima fase di espansione, seconda fase di compressione, seconda fase di espansione e infine terza fase di compressione. Nelle due fasi di espansione vengono applicate altrettante fasi di degasaggio sottovuoto per eliminare eventuali gas che si formano nella fase di fusione. Il doppio degasaggio è necessario quando si vuole processare un prodotto proveniente da rifiuto e con quantitativi d’inquinanti elevati.
Dopo l’ultimo stadio di compressione il materiale plastico fuso e degasato incontra un filtro autopulente per la rimozione delle ultime sostanze indesiderate quali residui di legno e di sughero. Sempre allo stato fuso le plastiche depurate dagli inquinanti passano nell’apposita matrice per essere poi tagliate. I granuli, derivati dalle plastiche leggere, sono poi raffreddati, asciugati e mediante aspirazione stoccati nel silo finale.
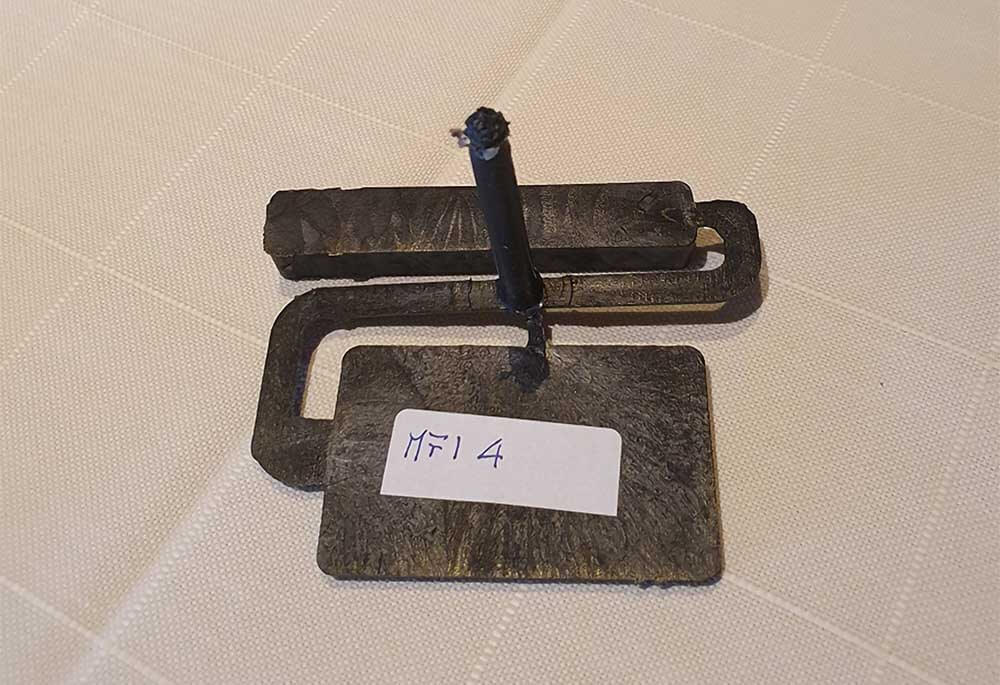
Prova stampaggio granulo con pressa a iniezione
A questo punto si ha un granulo plastico di colore grigio molto ricercato in diverse produzioni di particolari che vanno dai pallet per la logistica agli accessori per il garden. Essendo un granulo prodotto da un rifiuto, la composizione varia in base alla produzione a monte della cartiera, ma solo nelle percentuali. Per quanto riguarda la composizione delle plastiche, il processo ZWP assicura l’assenza di componenti indesiderate. Tutte le analisi DSC (Differential Scanning Calorimeter) effettuate su diversi campioni hanno sempre confermato l’assenza di PVC e una composizione a percentuale variabile di LDPE, HDPE e PP, con prevalenza delle ultime due plastiche.
In un momento congiunturale che vede una penuria di materie prime a tutti i livelli, avere la possibilità di recuperare una discreta quantità di materia prima secondaria, permette di cambiare le regole del gioco a favore della cartiera con minori costi di smaltimento e a favore del nostro pianeta mediante una riduzione sensibile di rifiuti dispersi nell’ambiente. Un vero e proprio esempio di “end of waste” e di economia circolare sostenibile.