Eine disruptive Lösung
Im Pulper Recyclingprozess aus Altpapier
Die Produktionsprozesse von Papierfabriken werden oft als umweltbelastende und umweltunempfindliche Aktivitäten bezeichnet, aber dank der kontinuierlichen technologischen Innovationen, die in den letzten Jahren in der Branche entwickelt wurden, gibt es auch bemerkenswerte Beispiele wie das Projekt zur Rückgewinnung von Leichtkunststoffen im Pulper Abfälle aus der Altpapierverarbeitung.
Das ZWP-Projekt wurde nach zwei Jahren der Erprobung und Tests mit der Installation eines kompletten Systems im Werk der Smurfit Kappa Group (ehemals BURGO GROUP) in Verzuolo CN abgeschlossen und brachte das Unternehmen an die Spitze des Umweltbewusstseins und der Nachhaltigkeit.
Das Unternehmen, das die Lösung implementiert, ist Hydroswiss, dem es nach mehrmonatigen Studien und Tests gelungen ist, leichte Kunststoffe, einen mit einem CER-Code gekennzeichneten Abfall, in einen zweiten Rohstoff umzuwandeln, dh Kunststoffgranulat, das der Norm UNI 10667 entspricht.
Aber gehen wir der Reihe nach vor. Bei der Verarbeitung von Altpapier entsteht aus der ersten Auflösephase des Papiers, die im Pulper stattfindet, ein sogenannter Pulper-Abfall. Der Anteil des Abfalls hängt natürlich von der Qualität des verwendeten Zellstoffs ab und erreicht bis zu 10 % der Gesamtmenge, wenn Papier aus der kommunalen Abfallsammlung verwendet wird.
Pulperabfall war schon immer sowohl ein wirtschaftliches als auch ein ökologisches Problem für die Papierfabrik. Die Menge an unerwünschten Elementen, die das gesammelte Altpapier ausmachen, variiert je nach Herkunft, ist aber trotz der Bemühungen der Recycler immer sehr erheblich.
Die Notwendigkeit, die Entsorgung aufgrund ihrer ständig steigenden Kosten so weit wie möglich zu vermeiden, zusammen mit den objektiven Schwierigkeiten, die Kunststofffraktionen durch Verbrennung in Energie umzuwandeln, ist es zweifellos ein ehrgeiziges Ziel, eine alternative und effektive Lösung für ihre Wiederverwertung zu finden gleichzeitig eine drohende Not.
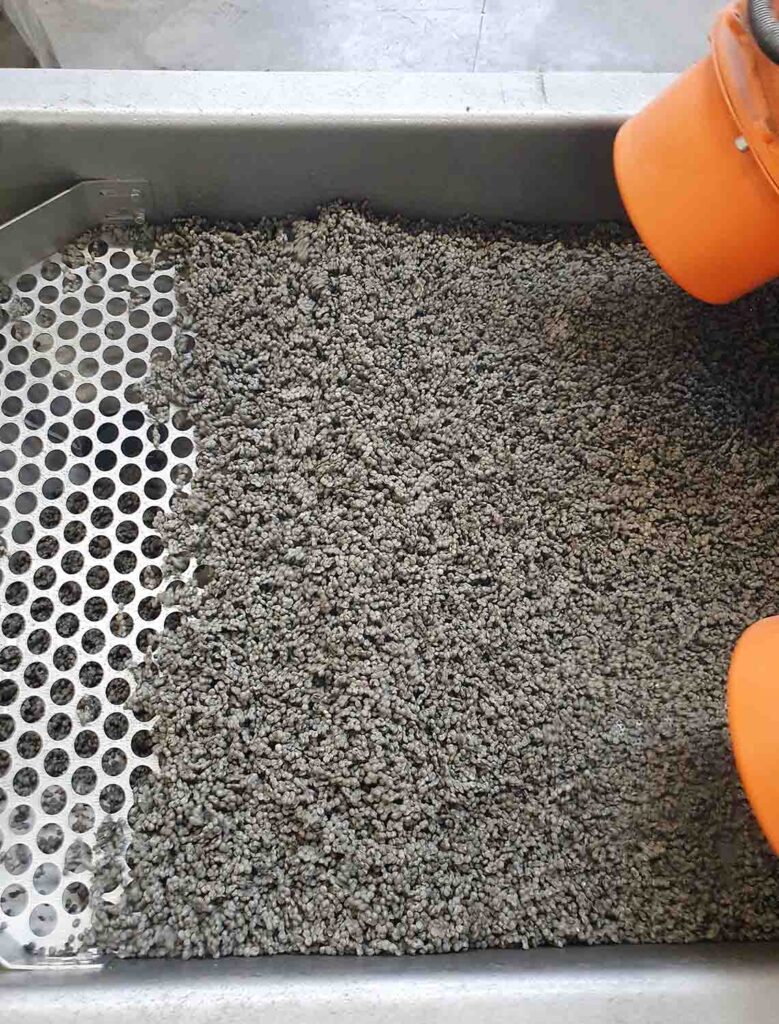
Pulperabfälle werden in der Siebstufe in Kunststoffgranulat umgewandelt
Die revolutionäre Lösung bestand darin, sowohl die wirtschaftlichen als auch die ökologischen Anforderungen des Werks zu erfüllen. Mit dem innovativen ZWP-Verfahren werden Pulperabfälle ausschließlich kaltmechanisch ohne Zusatz von Chemikalien in Sekundärrohstoffe (MPS) umgewandelt, mit Ausnahme des letzten Ziehprozesses, der bei Temperaturen um die 200°C stattfindet Kunststoffe schmelzen.
Beginnen wir mit dem Ergebnis. Der Pulperabfall als solcher besteht im Wesentlichen aus Wasser, Metallen, Kunststoffen, Textilien, Holz, Gummi und anderen inerten Materialien. Der Abfall gelangt in die Behandlungs- und Recyclinganlage, wo er verschiedene Stufen durchläuft, insgesamt etwa zwanzig, und gewaschen, standardisiert, erneut gewaschen und die verschiedenen wiederverwertbaren Materialien nach und nach getrennt werden in: Eisenmetalle, papierfaserhaltiges Wasser und leichte Kunststoffe (PE und PP); und die restlichen nicht recycelbaren Elemente wie: Inerte, schwere Kunststoffe und Nichteisenmetalle. Letztere können, wenn sie in erheblichen Mengen vorhanden sind, weiter aus dem Abfall extrahiert und recycelt werden. Das quantitative Ergebnis hängt von den Prozentsätzen der verschiedenen Elemente ab, die in die Anlage gelangen, aber im Durchschnitt beträgt die verbleibende Fraktion, die für das Recycling bestimmt ist, 10-15%,
Der Behandlungsverlauf. Im Wesentlichen wird die Pulper-Abfallverarbeitung in zwei Makrophasen unterteilt. Die erste besteht aus mehreren Wasch- und Volumenreduktionsprozessen, bei denen Eisenmetalle von nichtmagnetischen Metallen sowie allen Zuschlagstoffen und großformatigen schweren Kunststoffen getrennt werden. Alle Stufen werden mit Prozesswasser ergänzt, um ein effektives Waschen durchzuführen und die Papierfasern zurückzugewinnen, die in unter der Maschine positionierten Rinnen gesammelt und nach der Filtration in einen Tank geleitet werden, um später als Pulper-Einsatzmaterial in der Auflösestufe von verwendet zu werden Ballen.
In den letzten Stufen der ersten Phase werden die Schwimmstoffe, die hauptsächlich aus Kunststoffen, Holz, Gummi, Kork und kleinen Stoff- und Aluminiumstücken bestehen, zur anschließenden Trennung mit sauberem Prozesswasser weiter gewaschen. Diese letzte Trennstufe ermöglicht die Trennung der restlichen Partikel von schweren Kunststoffen (PVC) von leichten Kunststoffen (PE-PP). Erstere werden der Entsorgung zugeführt, während letztere den Behandlungsprozess fortsetzen, bei dem die Trennung vom Holz stattfindet, und schließlich einer Trocknungsphase unterzogen werden.
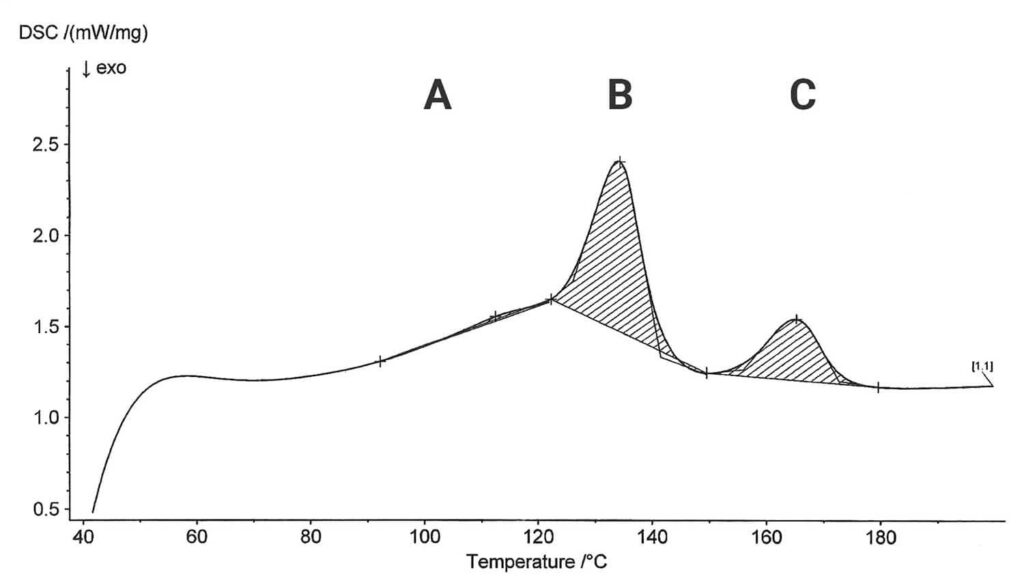
DSC Analyse:
A. 1% LDPE,
B. 63% HDPE,
C. 36% PP
Das Material, das die Anlage aus der ersten Behandlungsphase verlässt, besteht aus Konfetti mit einer Größe von 20-30 mm, das im Wesentlichen zu 90 % aus leichten Kunststoffen und zu 10 % aus restlichen unerwünschten Materialien wie Holz, Kork und einigen Aluminiumpartikeln besteht. Das Material wird zu diesem Zeitpunkt immer noch als Abfall betrachtet, obwohl es nicht gefährlich ist, und gemäß den Verfahren der Papierfabrik mit dem Code CER191204 oder CER150102 gekennzeichnet.
Die zweite Behandlungsphase besteht aus der eigentlichen Umwandlung des Restabfalls in Kunststoffgranulat gemäß der Norm UNI10667-15, einem echten Sekundärrohstoff, der verkauft werden kann. Während in der ersten Verarbeitungsphase einige Maschinen konstruiert werden mussten, die es auf dem Markt nicht gab, wurden in dieser zweiten Phase vorhandene Maschinen verwendet, an denen entsprechende Modifikationen vorgenommen wurden, um die aus der ersten Anlage kommenden Kunststoffe verarbeiten zu können .
Auch diese Phase besteht aus mehreren Stufen (neun), um die Kunststoffabfälle in Sekundärrohstoffe in Form von Granulat umzuwandeln. Das eingehende Material wird mit einem Metalldetektor überprüft, um zu verhindern, dass unerwünschte Metallpartikel in den Prozess gelangen. Anschließend gelangt das Material in einen Verdichter, der die Doppelfunktion hat, das 20–30 mm große Konfetti in noch kleinere und gleichmäßigere Partikel umzuwandeln und den Feuchtigkeitsgehalt auf unter 5 % zu reduzieren, den in den nachfolgenden Verarbeitungsstufen gewünschten Maximalwert.
Aus dem Verdichter wird das Kunststoffmaterial über ein gesteuertes Lamellenventil in die Extrusionsschnecke dosiert, wo das Aufschmelzen stattfindet. Die Extrusionsschnecke wiederum hat fünf aufeinanderfolgende Phasen: erste Kompressionsphase, erste Expansionsphase, zweite Kompressionsphase, zweite Expansionsphase und schließlich dritte Kompressionsphase. In den beiden Expansionsphasen wird die gleiche Anzahl von Vakuumentgasungsphasen angewendet, um eventuell in der Schmelzphase gebildete Gase zu beseitigen. Bei der Verarbeitung eines Produktes aus Abfall und mit hohen Schadstoffanteilen ist eine doppelte Entgasung erforderlich.
Nach der letzten Verdichtungsstufe trifft das geschmolzene und entgaste Kunststoffmaterial auf einen selbstreinigenden Filter, um letzte unerwünschte Stoffe wie Holz- und Korkreste zu entfernen. Noch im geschmolzenen Zustand gelangen die von Schadstoffen gereinigten Kunststoffe in die entsprechende Matrix, um anschließend geschnitten zu werden. Das aus den Leichtkunststoffen gewonnene Granulat wird anschließend gekühlt, getrocknet und im Endsilo abgesaugt.
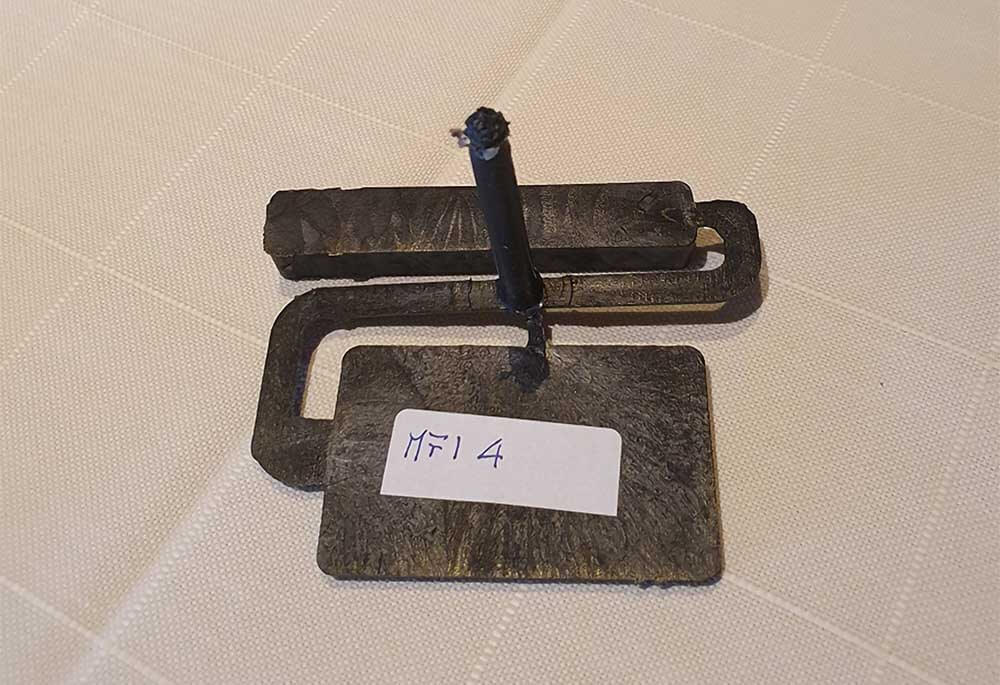
Granulatformtest mit Spritzgussmaschine
Das Material, das die Anlage aus der ersten Behandlungsphase verlässt, besteht aus Konfetti mit einer Größe von 20-30 mm, das im Wesentlichen zu 90 % aus leichten Kunststoffen und zu 10 % aus restlichen unerwünschten Materialien wie Holz, Kork und einigen Aluminiumpartikeln besteht. Das Material wird zu diesem Zeitpunkt immer noch als Abfall betrachtet, obwohl es nicht gefährlich ist, und gemäß den Verfahren der Papierfabrik mit dem Code CER191204 oder CER150102 gekennzeichnet.
Die zweite Behandlungsphase besteht aus der eigentlichen Umwandlung des Restabfalls in Kunststoffgranulat gemäß der Norm UNI10667-15, einem echten Sekundärrohstoff, der verkauft werden kann. Während in der ersten Verarbeitungsphase einige Maschinen konstruiert werden mussten, die es auf dem Markt nicht gab, wurden in dieser zweiten Phase vorhandene Maschinen verwendet, an denen entsprechende Modifikationen vorgenommen wurden, um die aus der ersten Anlage kommenden Kunststoffe verarbeiten zu können .
Auch diese Phase besteht aus mehreren Stufen (neun), um die Kunststoffabfälle in Sekundärrohstoffe in Form von Granulat umzuwandeln. Das eingehende Material wird mit einem Metalldetektor überprüft, um zu verhindern, dass unerwünschte Metallpartikel in den Prozess gelangen. Anschließend gelangt das Material in einen Verdichter, der die Doppelfunktion hat, das 20–30 mm große Konfetti in noch kleinere und gleichmäßigere Partikel umzuwandeln und den Feuchtigkeitsgehalt auf unter 5 % zu reduzieren, den in den nachfolgenden Verarbeitungsstufen gewünschten Maximalwert.
Aus dem Verdichter wird das Kunststoffmaterial über ein gesteuertes Lamellenventil in die Extrusionsschnecke dosiert, wo das Aufschmelzen stattfindet. Die Extrusionsschnecke wiederum hat fünf aufeinanderfolgende Phasen: erste Kompressionsphase, erste Expansionsphase, zweite Kompressionsphase, zweite Expansionsphase und schließlich dritte Kompressionsphase. In den beiden Expansionsphasen wird die gleiche Anzahl von Vakuumentgasungsphasen angewendet, um eventuell in der Schmelzphase gebildete Gase zu beseitigen. Bei der Verarbeitung eines Produktes aus Abfall und mit hohen Schadstoffanteilen ist eine doppelte Entgasung erforderlich.
Nach der letzten Verdichtungsstufe trifft das geschmolzene und entgaste Kunststoffmaterial auf einen selbstreinigenden Filter, um letzte unerwünschte Stoffe wie Holz- und Korkreste zu entfernen. Noch im geschmolzenen Zustand gelangen die von Schadstoffen gereinigten Kunststoffe in die entsprechende Matrix, um anschließend geschnitten zu werden. Das aus den Leichtkunststoffen gewonnene Granulat wird anschließend gekühlt, getrocknet und im Endsilo abgesaugt.