A disruptive solution
In the pulper recycling process from waste paper
The production processes of paper mills are often pointed out as polluting and environmentally insensitive activities, but thanks to the continuous technological innovations developed in the sector in recent years, there are also noteworthy examples such as the project for the recovery of light plastics in the pulper waste from waste paper processing.
The ZWP project saw its completion after two years of trials and tests, installing a complete system at the Smurfit Kappa Group (Ex BURGO GROUP) plant in Verzuolo CN, bringing the company to the top of environmental awareness and sustainability.
The company implementing the solution is Hydroswiss, which after several months of studies and tests has succeeded in converting light plastics, a waste identified with a CER code, into a second raw material, i.e. plastic granules complying with the UNI 10667 standard.
But let us proceed in order. The processing of waste paper produces a waste, called pulper waste, from the first pulping phase of the paper, which takes place inside the pulper. The percentage of waste obviously depends on the quality of the pulp used, reaching up to 10% of the total in the case of using paper from municipal waste collection.
Pulper waste has always been both an economic and an environmental problem for the paper mill. The amount of unwanted elements that make up the collected waste paper varies according to origin, but despite the efforts of the recyclers, it is always very significant.
The need to avoid disposal as much as possible, due to its ever-increasing costs, together with the objective difficulties of converting the plastic fractions into energy by combustion, finding an alternative and effective solution for recycling them is undoubtedly an ambitious goal and at the same time an impending need.
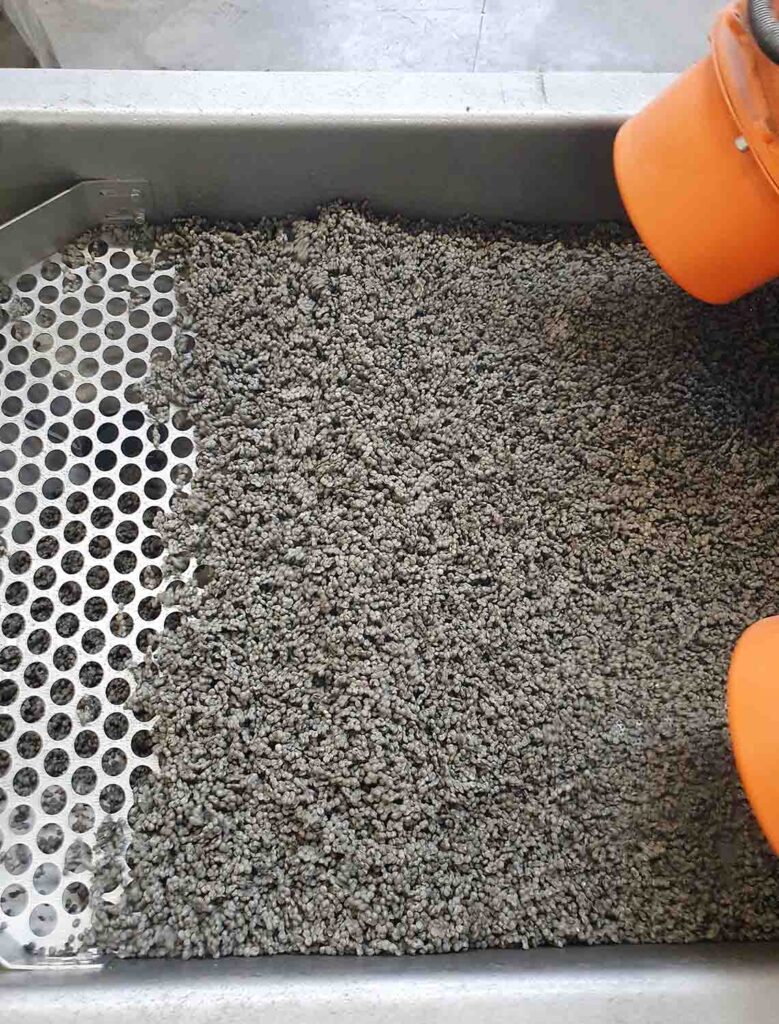
Pulper waste transformed into plastic granule at the screening stage
The disruptive solution was to meet both the mill’s economic and environmental demands. Using the innovative ZWP process, pulper waste is transformed into secondary raw materials (MPS) using only cold mechanical processes without the use of added chemicals, with the exception of the last drawing process, which takes place at temperatures around 200°C in order to melt the plastics.
Let us start with the result. The pulper waste as such is essentially composed of water, metals, plastics, textiles, wood, rubber and other inert materials. The waste enters the treatment and recycling plant, where it undergoes various stages, about twenty in total, and is washed, standardised, re-washed, and the various recyclable materials are gradually separated into: ferrous metals, water containing paper fibre and light plastics (PE and PP); and the remaining non-recyclable elements such as: inerts, heavy plastics and non-ferrous metals. The latter, if present in significant quantities, can be further extracted from the waste and recycled. The quantitative result depends on the percentages of the various elements entering the plant, but on average the remaining fraction destined for recycling is 10-15%, managing to recover 85-90% of the waste as it is.
The treatment process. Essentially, the pulper waste processing is divided into two macro-phases. The first consists of several washing and volumetric reduction processes from which ferrous metals are separated from non-magnetic metals, as well as all aggregates and large-format heavy plastics. All stages are supplemented with process water to carry out effective washing and to recover the paper fibre, which is collected in gutters positioned under the machinery and fed into a tank, after filtration, to be used later as pulper feed in the pulping stage of the bales.
In the last stages of the first phase, the floating material, consisting mainly of plastics, wood, rubber, cork and small pieces of fabric and aluminium, undergoes further washing with clean process water for subsequent separation. This last separation stage enables the separation of the remaining particles of heavy plastics (PVC) from light plastics (PE-PP). The former are sent for disposal, while the latter continue the treatment process where separation from wood takes place and finally undergo a drying stage.
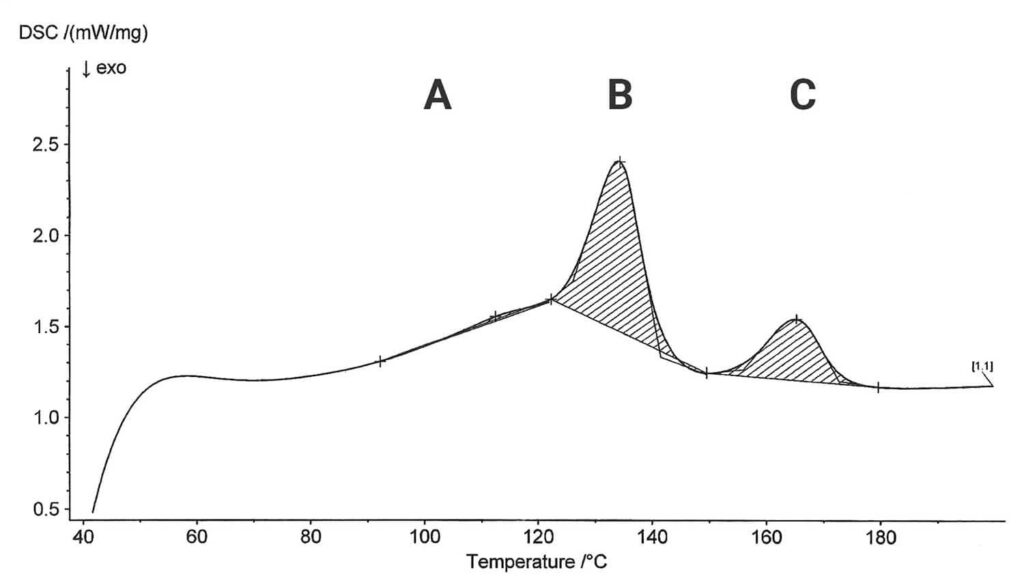
DSC analysis:
A. 1% LDPE,
B. 63% HDPE,
C. 36% PP
The material exiting the plant from the first treatment phase consists of confetti with a size of 20-30mm, essentially composed of 90% light plastics and 10% residual unwanted materials such as wood, cork and some aluminium particles. The material at this point is still considered waste, although not hazardous, identified with code CER191204 or CER150102 according to the paper mill’s procedures.
The second treatment phase consists of the actual transformation of the residual waste into plastic granules complying with the UNI10667-15 standard, a true secondary raw material that can be sold. While in the first treatment phase some machinery had to be designed that did not exist on the market, in this second phase, existing machinery was used to which appropriate modifications were applied in order to be able to process the plastics coming out of the first plant.
This phase also consists of several stages (nine) in order to convert the plastic waste into secondary raw material in the form of granules. The incoming material is checked using a metal detector to prevent unwanted metal particles from entering the process. Subsequently, the material enters a densifier, which has the dual function of transforming the 20-30mm confetti into even smaller and more uniform particles as well as reducing the moisture content below 5%, the maximum value desired in the subsequent processing stages.
From the densifier, the plastic material is dosed, via a controlled blade valve, into the extrusion screw where melting takes place. The extrusion screw, in turn, has five phases in sequence: first compression phase, first expansion phase, second compression phase, second expansion phase and finally third compression phase. In the two expansion phases, the same number of vacuum degassing phases are applied to eliminate any gases formed in the melt phase. Double degassing is necessary when processing a product from waste and with high amounts of pollutants.
After the last compression stage, the molten and degassed plastic material encounters a self-cleaning filter to remove the last undesirable substances such as wood and cork residues. Still in the molten state, the plastics purified of pollutants pass into the appropriate matrix to be then cut. The granules, derived from the lightweight plastics, are then cooled, dried and by suction stored in the final silo.
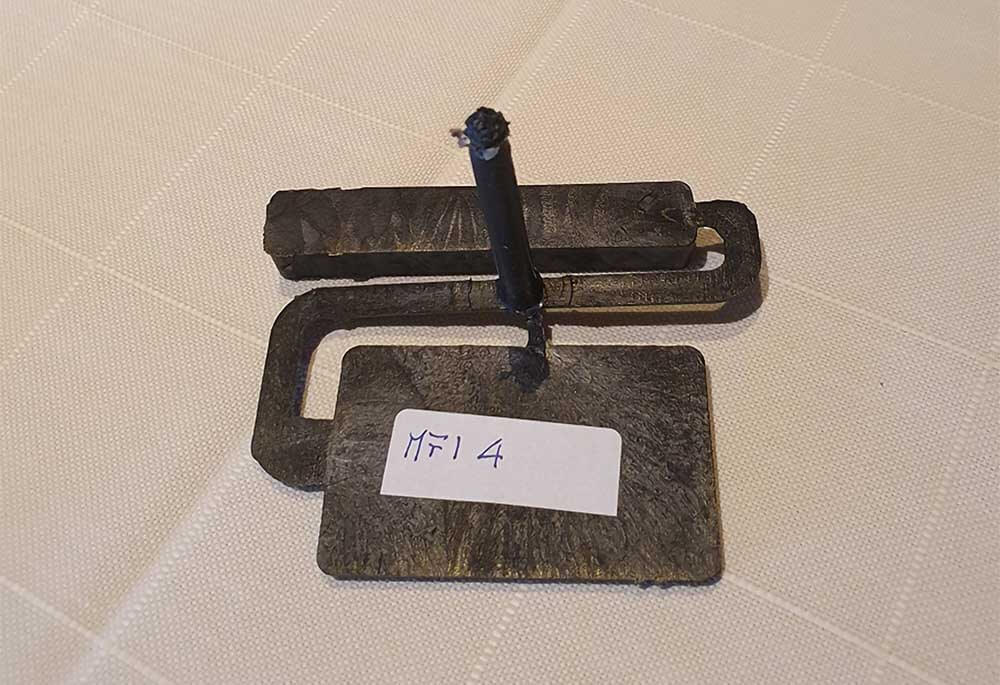
Granule moulding test with injection moulding machine
At this point, we have a grey-coloured plastic granule that is highly sought after in various parts productions ranging from logistics pallets to garden accessories. Being a granule produced from waste, the composition varies according to the upstream production of the paper mill, but only in percentages. As far as the composition of the plastics is concerned, the ZWP process ensures the absence of undesirable components. All DSC (Differential Scanning Calorimeter) analyses carried out on various samples have always confirmed the absence of PVC and a varying percentage composition of LDPE, HDPE and PP, with the last two plastics prevailing.
At a time when there is a scarcity of raw materials at all levels, having the possibility of recovering a fair amount of secondary raw material allows us to change the rules of the game in favour of the paper mill with lower disposal costs and in favour of our planet through a significant reduction of waste dispersed in the environment. A true example of ‘end of waste’ and sustainable circular economy.