Une solution disruptive
Dans le processus de recyclage du pulpeur à partir de vieux papiers
Les processus de production des papeteries sont souvent pointés du doigt comme des activités polluantes et insensibles à l’environnement, mais grâce aux innovations technologiques continues développées dans le secteur ces dernières années, il existe également des exemples notables tels que le projet de récupération des plastiques légers dans le pulpeur déchets issus du traitement des vieux papiers.
Le projet ZWP a vu son achèvement après deux ans d’essais et de tests, installant un système complet à l’usine du groupe Smurfit Kappa (Ex BURGO GROUP) à Verzuolo CN, amenant l’entreprise au sommet de la conscience environnementale et de la durabilité.
La société implémentant la solution est Hydroswiss, qui après plusieurs mois d’études et de tests a réussi à transformer les plastiques légers, un déchet identifié par un code CER, en une deuxième matière première, à savoir des granulés de plastique conformes à la norme UNI 10667.
Mais procédons dans l’ordre. Le traitement des vieux papiers produit un déchet, appelé déchet de pulpeur, dès la première phase de réduction en pâte du papier, qui a lieu à l’intérieur du pulpeur. Le pourcentage de déchets dépend évidemment de la qualité de la pâte utilisée, atteignant jusqu’à 10% du total dans le cas de l’utilisation de papier provenant de la collecte des déchets municipaux.
Les déchets de pâte à papier ont toujours été un problème à la fois économique et environnemental pour l’usine de papier. La quantité d’éléments indésirables qui composent les vieux papiers collectés varie selon l’origine, mais malgré les efforts des recycleurs, elle est toujours très importante.
La nécessité d’éviter autant que possible l’élimination, en raison de ses coûts toujours croissants, ainsi que les difficultés objectives de convertir les fractions plastiques en énergie par combustion, trouver une solution alternative et efficace pour les recycler est sans aucun doute un objectif ambitieux et à la base en même temps un besoin imminent.
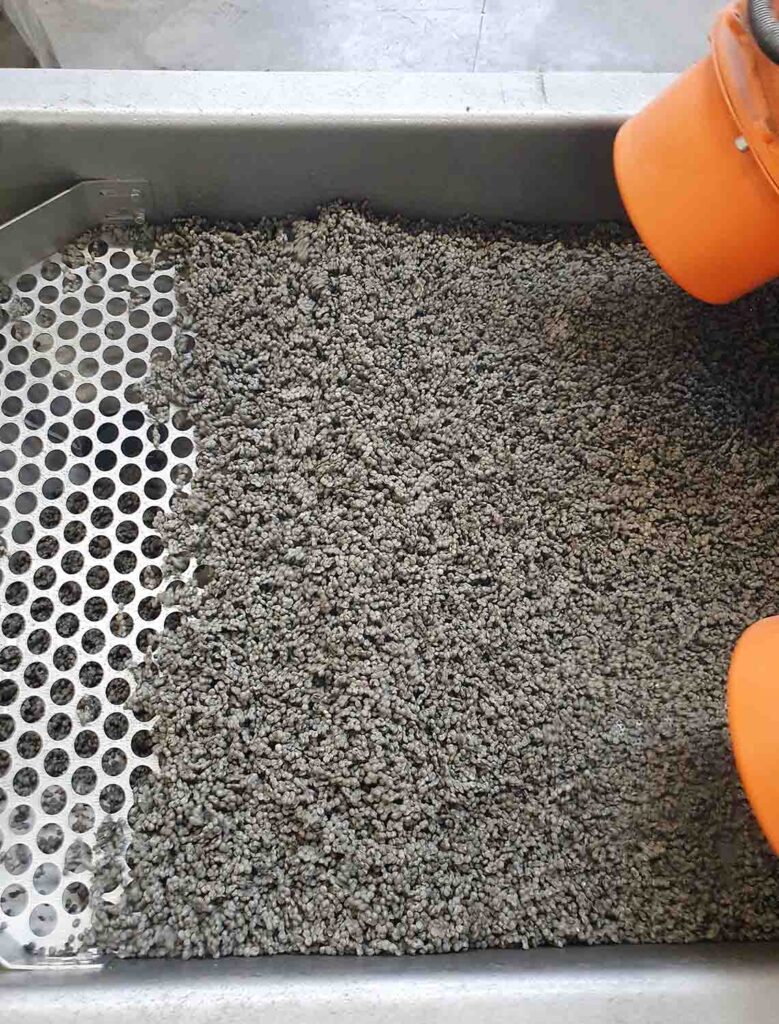
Déchets de pulpe transformés en granulés plastiques au stade du criblage
La solution de rupture consistait à répondre à la fois aux exigences économiques et environnementales de l’usine. Grâce au procédé innovant ZWP, les déchets de pulpage sont transformés en matières premières secondaires (MPS) en utilisant uniquement des procédés mécaniques à froid sans l’utilisation de produits chimiques ajoutés, à l’exception du dernier procédé d’étirage, qui a lieu à des températures d’environ 200°C afin de faire fondre les plastiques.
Commençons par le résultat. Les déchets de trituration en tant que tels sont essentiellement composés d’eau, de métaux, de plastiques, de textiles, de bois, de caoutchouc et d’autres matériaux inertes. Les déchets entrent dans l’usine de traitement et de recyclage, où ils subissent différentes étapes, une vingtaine au total, et sont lavés, standardisés, relavés, et les différentes matières recyclables sont progressivement séparées en : métaux ferreux, eau contenant des fibres de papier et des plastiques légers (PE et PP); et les autres éléments non recyclables tels que : les inertes, les plastiques lourds et les métaux non ferreux. Ces derniers, s’ils sont présents en quantités importantes, peuvent être extraits davantage des déchets et recyclés. Le résultat quantitatif dépend des pourcentages des différents éléments entrant dans l’usine, mais en moyenne la fraction restante destinée au recyclage est de 10-15%,
Le processus de traitement. Essentiellement, le traitement des déchets du pulpeur est divisé en deux macro-phases. Le premier consiste en plusieurs procédés de lavage et de réduction volumétrique à partir desquels les métaux ferreux sont séparés des métaux amagnétiques, ainsi que tous les granulats et plastiques lourds de grand format. Toutes les étapes sont complétées par de l’eau de procédé pour effectuer un lavage efficace et récupérer la fibre de papier, qui est collectée dans des gouttières placées sous la machine et introduite dans un réservoir, après filtration, pour être utilisée plus tard comme alimentation du pulpeur dans l’étape de réduction en pâte de la balles.
Dans les dernières étapes de la première phase, le matériau flottant, composé principalement de plastique, de bois, de caoutchouc, de liège et de petits morceaux de tissu et d’aluminium, subit un lavage supplémentaire avec de l’eau de traitement propre pour une séparation ultérieure. Cette dernière étape de séparation permet de séparer les particules restantes de plastiques lourds (PVC) des plastiques légers (PE-PP). Les premiers sont envoyés à l’élimination, tandis que les seconds poursuivent le processus de traitement où la séparation du bois a lieu et subissent enfin une étape de séchage.
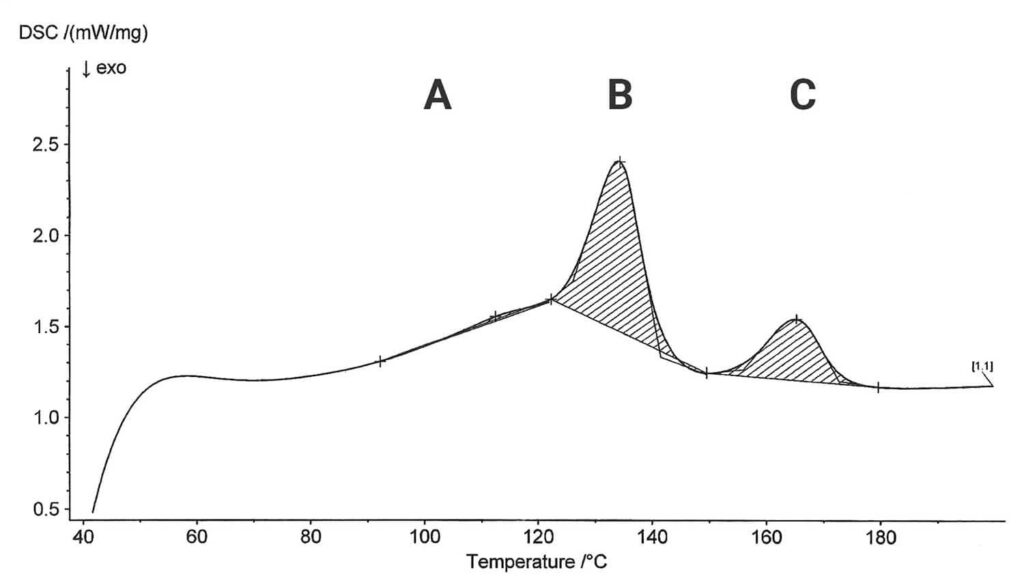
Analyse DSC :
A. 1% LDPE,
B. 63% HDPE,
C. 36% PP
Le matériau sortant de l’usine de la première phase de traitement est constitué de confettis d’une taille de 20 à 30 mm, essentiellement composés de 90 % de plastiques légers et de 10 % de matériaux résiduels indésirables tels que le bois, le liège et certaines particules d’aluminium. Le matériau à ce stade est toujours considéré comme un déchet, bien que non dangereux, identifié avec le code CER191204 ou CER150102 selon les procédures de la papeterie.
La deuxième phase de traitement consiste en la transformation proprement dite des déchets résiduels en granulés plastiques conformes à la norme UNI10667-15, véritable matière première secondaire commercialisable. Alors que dans la première phase de traitement, il a fallu concevoir des machines qui n’existaient pas sur le marché, dans cette deuxième phase, des machines existantes ont été utilisées auxquelles des modifications appropriées ont été appliquées afin de pouvoir traiter les plastiques sortant de la première usine. .
Cette phase comprend également plusieurs étapes (neuf) afin de transformer les déchets plastiques en matière première secondaire sous forme de granulés. Le matériau entrant est contrôlé à l’aide d’un détecteur de métaux pour empêcher les particules métalliques indésirables d’entrer dans le processus. Par la suite, le matériau entre dans un densificateur, qui a la double fonction de transformer les confettis de 20-30 mm en particules encore plus petites et plus uniformes ainsi que de réduire la teneur en humidité en dessous de 5 %, la valeur maximale souhaitée dans les étapes de traitement ultérieures.
A partir du densificateur, la matière plastique est dosée, via une vanne à lame contrôlée, dans la vis d’extrusion où la fusion a lieu. La vis d’extrusion, quant à elle, comporte cinq phases successives : première phase de compression, première phase d’expansion, deuxième phase de compression, deuxième phase d’expansion et enfin troisième phase de compression. Dans les deux phases de détente, le même nombre de phases de dégazage sous vide est appliqué pour éliminer les éventuels gaz formés en phase fondue. Un double dégazage est nécessaire lors du traitement d’un produit issu de déchets et avec de fortes quantités de polluants.
Après la dernière étape de compression, la matière plastique fondue et dégazée rencontre un filtre autonettoyant pour éliminer les dernières substances indésirables telles que les résidus de bois et de liège. Toujours à l’état fondu, les plastiques épurés des polluants passent dans la matrice appropriée pour être ensuite découpés. Les granulés, dérivés des plastiques légers, sont ensuite refroidis, séchés et stockés par aspiration dans le silo final.
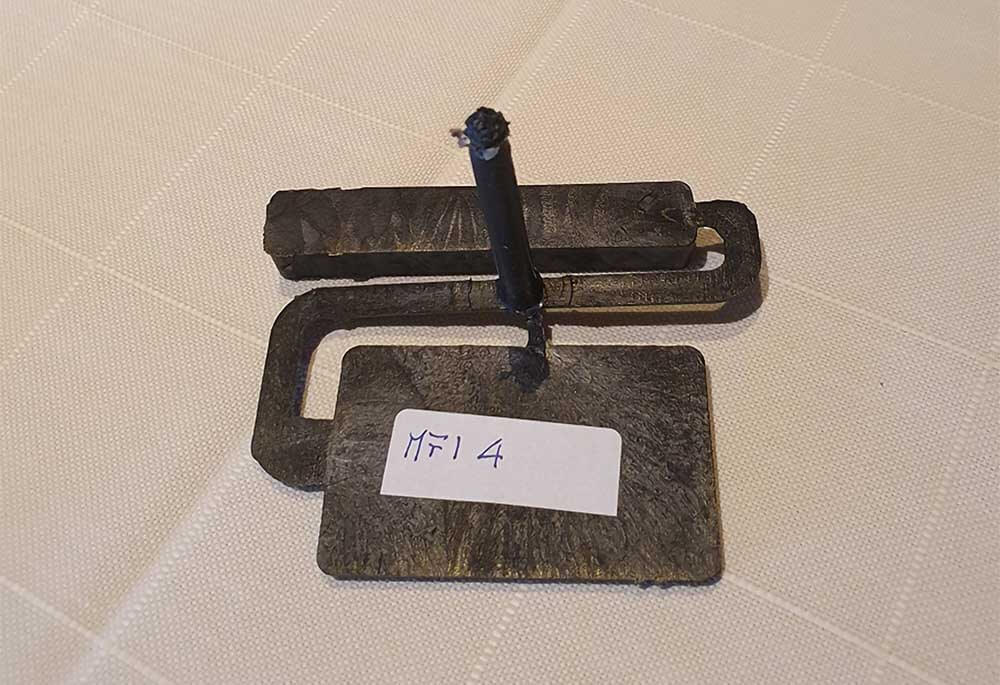
Test de moulage de granulés avec machine de moulage par injection
À ce stade, nous avons un granulé de plastique de couleur grise très recherché dans diverses productions de pièces allant des palettes logistiques aux accessoires de jardin. S’agissant d’un granulé produit à partir de déchets, sa composition varie selon la production en amont de la papeterie, mais uniquement en pourcentage. En ce qui concerne la composition des plastiques, le procédé ZWP garantit l’absence de composants indésirables. Toutes les analyses DSC (Differential Scanning Calorimeter) effectuées sur différents échantillons ont toujours confirmé l’absence de PVC et une composition en pourcentage variable de LDPE, HDPE et PP, les deux derniers plastiques prédominant.
A l’heure de la raréfaction des matières premières à tous les niveaux, avoir la possibilité de récupérer une bonne quantité de matière première secondaire nous permet de changer les règles du jeu en faveur de la papeterie à moindre coût d’élimination et en faveur de notre planète grâce à une réduction significative des déchets dispersés dans l’environnement. Un véritable exemple de « fin des déchets » et d’économie circulaire durable.